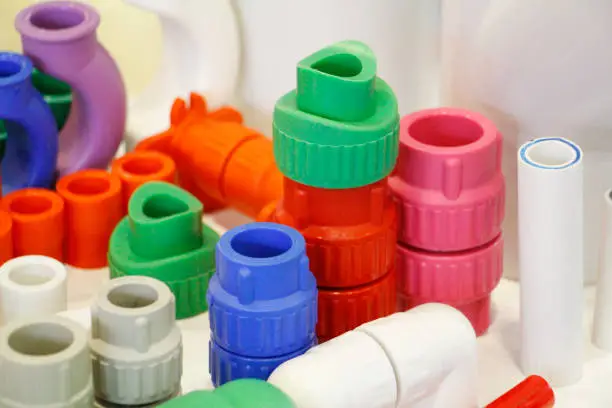
Acrylonitrile Butadiene Styrene (ABS) is a widely used thermoplastic polymer known for its excellent impact resistance, toughness, and ease of processing. Due to these superior properties, ABS is widely used in various industries, including automotive, medical, consumer electronics, and household appliances. The ABS injection molding requires precise control over material handling, temperature, pressure, and cooling to ensure high-quality molded products. This article will cover the key steps, best practices, and solutions to common ABS molding defects to optimize manufacturing results.
What is ABS Plastic?
ABS is an engineering thermoplastic with a balance of strength, rigidity, and processability. Some of its key characteristics include:
- High impact resistance and toughness for durable products
- Good dimensional stability to maintain part accuracy
- Strong resistance to chemicals and heat
- Excellent surface finish and paintability
- Good electrical insulation properties, making it ideal for electronic components
These properties make ABS ideal for producing automotive parts, electronic enclosures, medical devices, and household goods.
ABS Injection Molding Process
ABS (Acrylonitrile Butadiene Styrene) is a popular thermoplastic used in injection molding due to its excellent strength, toughness, and surface finish. Here’s an overview of the injection molding process specifically tailored for ABS material:
Machine Requirements
ABS can be molded using standard injection molding machines, but the following conditions are important to ensure optimal results:
-
Screw Type: General-purpose screw with a compression ratio of 2.5–3.0
-
Injection Pressure: Typically 70–120 MPa
-
Clamping Force: Medium to high, depending on part size and complexity
-
Drying Requirements: ABS must be dried at 80–90°C for at least 2–4 hours before processing to avoid moisture bubbles or silver streaks
Processing Temperature Range
Temperature control is critical when molding ABS, as it is sensitive to degradation if overheated.
Zone | Recommended Temperature |
---|---|
Feed Zone | 190 – 210°C |
Compression Zone | 210 – 230°C |
Metering Zone | 220 – 250°C |
Nozzle | 220 – 250°C |
Mold Temperature | 60 – 80°C |
Maintaining stable and uniform temperature is essential to prevent warping, surface defects, and internal stress.
Injection Pressure & Speed
-
Injection Pressure: 70–120 MPa
-
Holding Pressure: 40–60% of injection pressure
-
Injection Speed: Medium to fast (slower speeds may cause weld lines; faster speeds can help achieve better surface finish)
Shrinkage
ABS has a relatively low shrinkage rate, typically between 0.4% – 0.7% depending on:
-
Wall thickness
-
Mold design
-
Gate type and size
-
Fill rate and pressure
Proper cooling time and uniform mold temperature are crucial to minimize warping and ensure dimensional stability.
Advantages of ABS Injection Molding
ABS is a widely used engineering thermoplastic, especially popular in automotive, consumer electronics, and medical device industries. Its combination of mechanical strength, aesthetic quality, and processing ease makes it ideal for injection molding.
1. High Impact Resistance
ABS offers excellent toughness and impact strength, making it suitable for parts that require durability under mechanical stress. This makes it ideal for products like:
-
Protective housings and enclosures
-
Automotive interior components
-
Handheld device cases
Even at low temperatures, ABS maintains impact resistance, making it reliable for both indoor and outdoor applications.
2. Excellent Surface Finish
One of ABS’s standout qualities is its smooth surface finish and good gloss. This allows molded parts to be:
-
Easily painted, plated, or silk-screened
-
Used directly in consumer-facing applications without secondary processing
-
Made with intricate surface details (thanks to its good flow characteristics)
This is why ABS is often used in aesthetic components of electronics, such as remote controls or appliance panels.
3. Recyclability
ABS is a thermoplastic, meaning it can be melted down and reprocessed without significant degradation. Its recyclability offers:
-
Lower material costs through reuse of regrind
-
Reduced environmental impact
-
Easier waste management in high-volume production
Industries increasingly value ABS for sustainable manufacturing due to its recyclability and low VOC emissions.
Applications of ABS Injection Molding
ABS injection molding is widely used in various industries, including:
- Medical Industry: Equipment housings, diagnostic device components
- Automotive Industry: Dashboards, interior trims, and bumper components
- Consumer Electronics: Laptop cases, keyboard frames, and remote controls
- Household Appliances: Vacuum cleaner parts, refrigerator liners, and tool housings
Optimal ABS Injection Molding Parameters
a. Temperature Settings
Proper temperature control ensures uniform melting and prevents molding defects.
- Barrel temperature: 200–250°C (392–482°F)
- Nozzle temperature: Slightly lower than barrel temperature to prevent drooling
- Mold temperature: 50–80°C (122–176°F), depending on part thickness
b. Injection Speed and Pressure
- Injection pressure: 10–20 MPa (1450–2900 psi)
- Holding pressure: 30–50% of the injection pressure
- Injection speed: Medium to high to ensure proper flow into the mold cavities
- Back pressure: 0.3–4 MPa to ensure uniform melting
c. Cooling Time and Ejection
- Cooling time: 20–60 seconds depending on part thickness
- Ejection system: ABS parts should be properly cooled before ejection to avoid deformation
Common ABS Molding Defects and Solutions
1. Bubbles or Silver Streaks
- Cause: Excess moisture in ABS material
- Solution: Ensure proper drying before processing
2. Burn Marks
- Cause: Overheating due to high injection speed or prolonged residence time
- Solution: Lower the barrel temperature and adjust injection speed
3. Short Shots
- Cause: Insufficient injection pressure or low temperature
- Solution: Increase injection pressure and ensure proper melt temperature
4. Flashing
- Cause: Excessive injection pressure or improper mold clamping
- Solution: Optimize pressure settings and check mold alignment
ABS Injection Molding at XLD Mould
At XLD Mould, we are committed to delivering high-precision ABS injection molding solutions that meet the most demanding industry standards. Our expertise ensures:
- Custom mold design and engineering for enhanced performance and efficiency
- Material selection guidance to ensure optimal functionality and durability
- Advanced injection molding process optimization to achieve consistent, high-quality results
- Comprehensive defect prevention strategies to minimize waste and maximize productivity
With our state-of-the-art manufacturing capabilities and a dedicated team of experts, XLD Mould guarantees superior ABS injection molding services tailored to your specific needs.
📞 Contact us today to discuss your ABS molding project and let us provide you with innovative, cost-effective injection molding solutions.